What Makes Diamond Blades a Better Choice than Abrasive Blades!
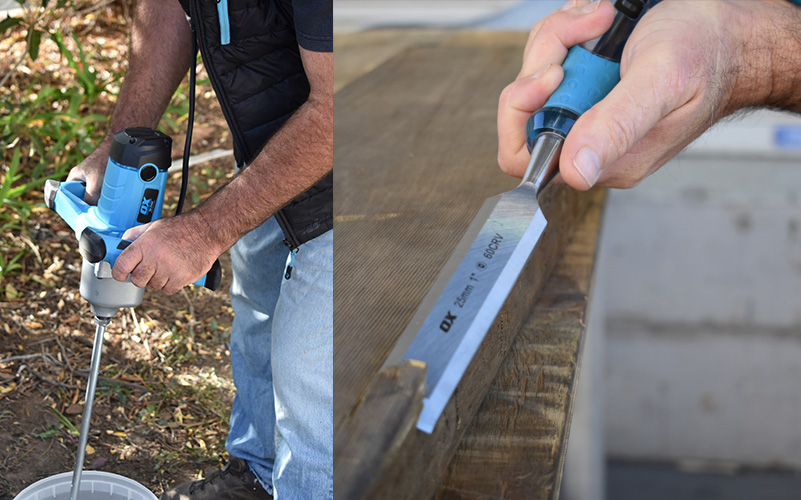
From stone to cement and clay to tiles, a engineering site has an selection of materials that require to be cut regularly. Such strong materials require an similarly solid slicing tool. While Abrasive Blades have been trusted across various reducing responsibilities, it’s the Diamond Blades that are actually the preferred selection of every tradie. Diamond Blades certainly credit score over Abrasive Blades as it pertains to making clean, professional slices on any surface. Quality aside, it’s just how these blades are made is what units them aside. Let’s take a closer look.
Abrasive Blades
Abrasive Blades are created using hard material compounds like aluminum oxide and silicon carbide, that are then fused with resin to create a blade. While these metals may seem to be hard, but as the blade is spun at a higher quickness, they wear-off and induce a cut over a surface.
Disadvantages of Using Abrasive Blades
This cutting process wears the blade prematurely, reducing the life of the Abrasive Blade. With repetitive use, these blades have a tendency to lose their structural integrity and may break aside, endangering the life span of an individual or those across the working area. The Occupational Safeness and Health Administration (OSHA) has numerous information of injuries and deaths caused by shattering Abrasive Blades.
Another reason Abrasive Blades are less popular is the fact that it emits dangerous substances like silicon and carbide fibers with all the blade. Another reason Abrasive Blades are less in demand is the fact it emits dangerous substances like silicon and carbide fibres with all the blade. Silica is highly carcinogenic when inhaled and frequent exposure to such chemicals might lead to silicosis and perhaps, even lung cancers.
Diamond Blades
Diamond Blades are created using synthetic Gemstone Crystals and are held set up by a designed mixture of various metals which determine the speed of which the diamonds crystals are exposed. A harder relationship between the Diamond jewelry and the metal reduces Diamonds erosion, which is suitable for softer applications like renewable concrete or asphalt. A softer relationship increases Gem erosion and it is most effective for harder materials such as granite or cured concrete.
Manufacturing Process
The Gemstone Crystals and bonding metal are heated, shaped, and mounted on the blade core, which is manufactured out of high alloy, heat-treated steel. The eventual edge of the Gemstone Edge can either be segmented, constant rimmed, or serrated. In each circumstance, the Diamond edge is wider than the blade’s core, in reducing drag on the blade and increase materials removal, and reduce the chance of cutting tool binding within the material, thereby producing a fine chop. These ends are affixed to the metal core through the brazing, sintering or laser beam welding process.
Benefits of Using Stone Blades
Unlike Abrasive Rotor blades, Diamond Rotor blades use friction that is established between the Diamonds and the cutting surface to make a precise cut.
Because of its strong construction, Diamond Cutting blades are safer to use than Abrasive Rotor blades, as they don’t wear to make a slash, won’t break aside nor do they emanate silicon or carbide dietary fiber while functioning.
Quality Matters
However when it involves pure performance, quality Diamond Blades is the thing you need. Low-cost Gem Rotor blades often use Gem corners that are welded onto the core. This cost-saving method not only reduces the life of the edge but escalates the threat of breaking while used and could possibly cause fatal injuries to the user.
Laser-welded Diamond Blades will tend to have an extended life and slashed faster than sintered or welded Diamond Blades. The laser welding process with Stone Blades flame the sections onto the core. This leaves the bond much more robust and produces a much better quality product.
As Diamond Rotor blades OX Tools are greater than those for Abrasive Rotor blades, it’s the life and quality of edge that eventually decides the go back of your investment. Abrasive Cutting blades have a shorter life expectancy and are
not effective for cutting harder materials. This means you have to displace your rotor blades faster. Diamond Rotor blades, on the other hand, have an extended shelf life and perform superlatively on all surfaces. Therefore your initial investment will pay-off in the end invest the proper care of your blade.